How to improve the heat transfer coefficient of heat exchanger
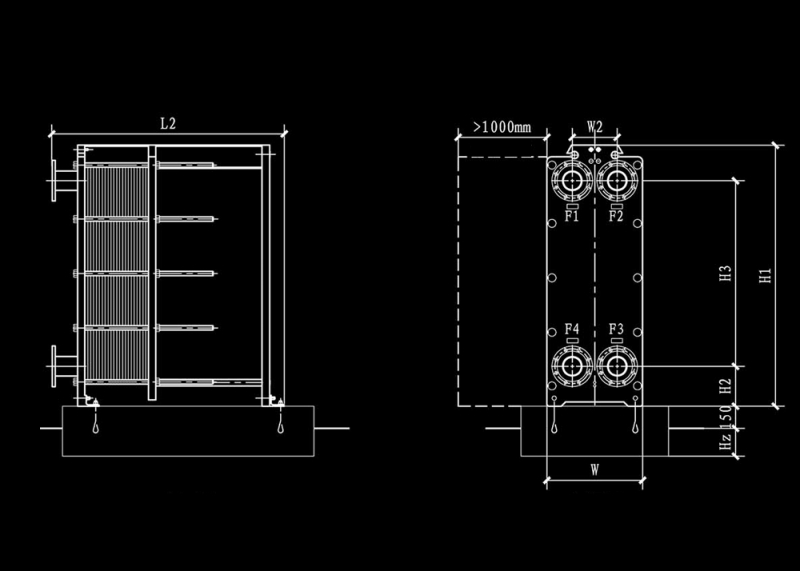
I believe that everyone has a certain understanding of the knowledge of heat exchangers. When using them, you should understand the heat transfer coefficient of the heat exchanger, The following heat exchanger manufacturers will give you a detailed introduction:
1, reduce the thermal resistance of the dirt layer
The key to reducing the thermal resistance of the fouling layer of the heat exchanger is to prevent fouling of the plates. When the plate fouling thickness is 1mm, the heat transfer coefficient of the heat exchangers reduced by about 10%. Therefore, it is important to monitor the water quality on both sides of the heat exchanger to prevent fouling of the plates and prevent debris in the water from adhering to the plates. In order to prevent water theft and corrosion of steel parts, some heating units add chemicals to the heating medium. Therefore, it is necessary to pay attention to the water quality and viscous chemicals that cause debris to contaminate the heat exchanger plates. If there are viscous debris in the water, special filters should be used for treatment. When choosing medicines, it is advisable to choose non-sticky medicines.
2, reduce the thickness of the plate
The design thickness of the plate has nothing to do with its corrosion resistance, but is related to the pressure-bearing capacity of the heat exchanger. Thicker plates can improve the pressure-bearing capacity of the heat exchanger. When the herringbone plate combination is adopted, the adjacent plates are turned upside down, and the corrugations are in contact with each other, forming a fulcrum with high density and uniform distribution. The corners of the plates and the edge sealing structure have been gradually improved, making the heat exchanger have a good Pressure endurance.
3, improve the surface heat transfer coefficient of the plate
Because the corrugation of the heat exchanger can cause the fluid to produce turbulence at a small flow rate (Reynolds number-150), it can obtain a higher surface heat transfer coefficient, which is related to the geometric structure of the plate corrugation and the medium The flow status is related. The waveform of the plate includes herringbone, straight, spherical and so on.
4. Use plates with high thermal conductivity
The plate material can choose austenitic stainless steel, titanium alloy, copper alloy, etc. Stainless steel has good thermal conductivity, with a thermal conductivity of about 14.4W/(m·K), high strength, good stamping performance, and is not easy to be oxidized. The price is lower than that of titanium alloy and copper alloy. It is used more in heating engineering, but it is resistant The ability of chloride ion to corrode is poor.
For heat exchangers, the heat transfer coefficient of the heat exchanger plays an important role in the equipment. In order to improve the heat transfer coefficient of the heat exchanger, it is necessary to find the reasons that affect the heat transfer coefficient of the heat exchanger. Ways to improve.